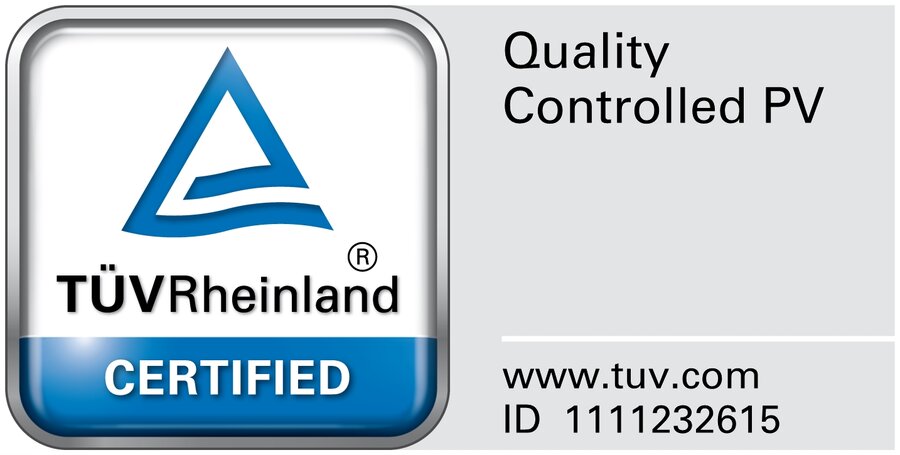
Quality Controlled PV
TÜV seal for the most reliable
Qcells is the first and so far only manufacturer of solar modules to participate in the most comprehensive quality programme in the industry: The new “Quality Controlled PV” of the independent certification institute TÜV Rheinland.
The new “Quality Controlled PV” of the independent certification institute TÜV Rheinland. We continuously test our solar modules in mass production far beyond the usual approval certification in accordance with the future IEC TS 63209 – the “Extended Stress Test for PV Modules” – and also monitor materials and component suppliers.
With “Quality Controlled PV” from TÜV Rheinland, we prove the permanent high safety and quality of our solar modules and ensure our customers high yields over the life of the module.
1. Extended Stress Test in line with future IEC TS 63209
This series of over 40 individual tests puts our solar modules to the test: Before we go into series production and after any change – no matter how minor – we carry out module tests that set new industry standards.
2. Continuous production monitoring
This is unique in the industry: In order to be able to guarantee product stability, we regularly carry out spot checks on our product lines. In addition to this, an employee of TÜV Rheinland continuously monitors the Qcells quality and monitoring measures at all Qcells production sites.
3. Component and material tests
Using special analysis methods, we regularly check particularly critical components and materials at goods receipt in order to detect any quality fluctuations at an early stage, thereby keeping them out of production. In this way, we can also avoid errors that would not be visible even in tough climatic chamber tests.
Our test scenarios
Our aim is to ensure the highest level of confidence in the reliability of our solar modules and to guarantee long life cycles. That is why we are currently the only manufacturer to rely on the 3-part test programme “Quality Controlled PV” of TÜV Rheinland.
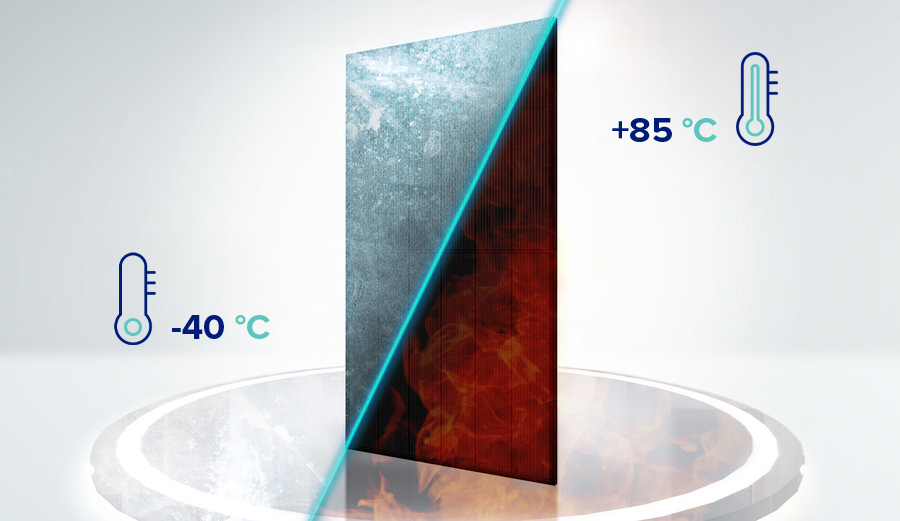
TC 600: 600 times from the south pole to the Sahara and back
Only solar modules from Qcells go through 600 cycles with temperature changes from -40 °C to +85 °C within 15 weeks. This is 3 times harder than the IEC test TC 200. In this we, we ensure that the soldering guns in the modules last 25 years even in the toughest locations in the world.
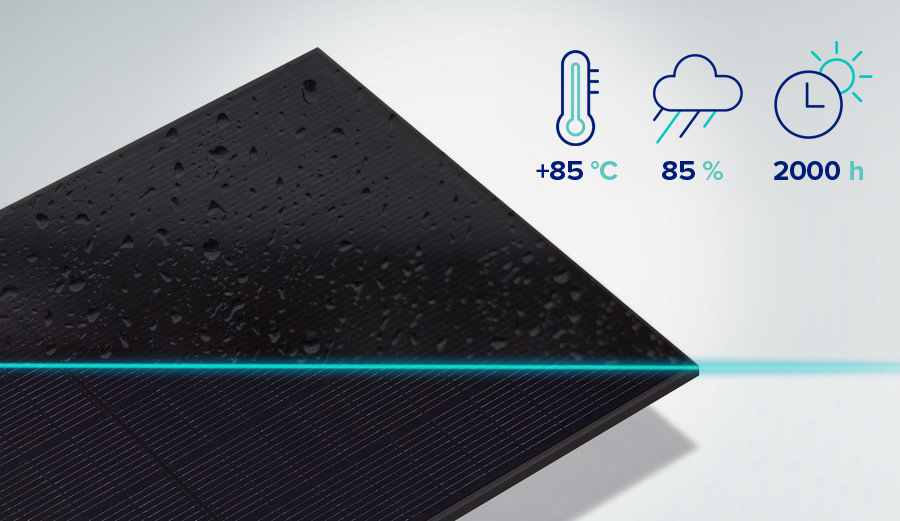
DH 2000: 2,000 hours climate chamber
We put our solar modules to the test for twice as long as the IEC certification requires: They spend 2,000 hours in the climate chamber at 85 °C and 85 % relative humidity to meet our high quality standards. By exposing our solar modules to these extreme conditions, we ensure that they can withstand any climate and thus recognise early on whether materials are suitable. Without QCPV, this would only be discovered very late – possibly even during operation.
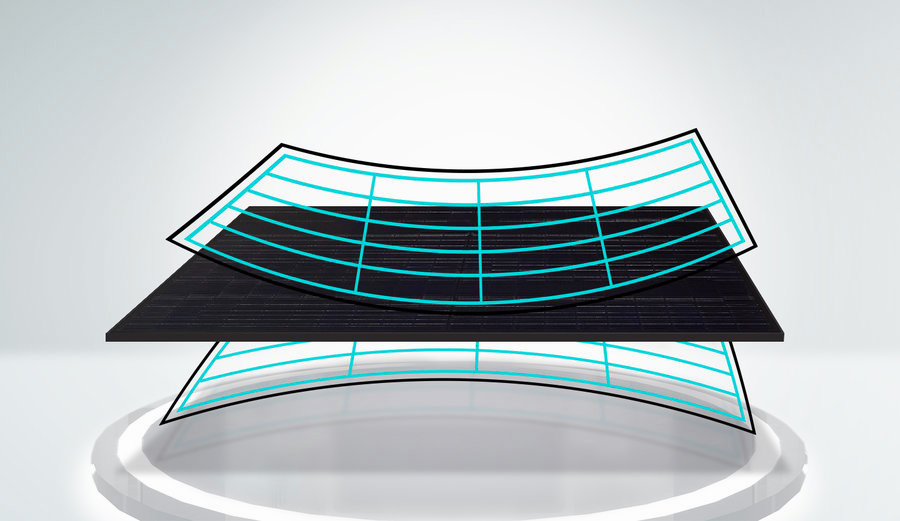
Load and degradation tests
Our solar modules are at the forefront of these tests: the solar modules must prove that they meet our strict requirements. Among other things, they have to demonstrate their mechanical resilience under extreme wind and snow load conditions in the laboratory. The long-term resistance of the plastics used is also tested in climate chambers under warm and humid conditions (85 °C / 85 % humidity). Temperature changes simulated in other climate chambers (-40 °C to 85 °C) test the reliability of the solder connections in the module. In addition, important reliability tests are carried out during these tests, which are not yet reflected in the current IEC certifications (PID, LeTID). In order to make the test conditions even more realistic, various climate chamber tests based on the latest scientific findings are also carried out successively in defined sequences. This ensures that our modules can withstand all real weather conditions for a long time.
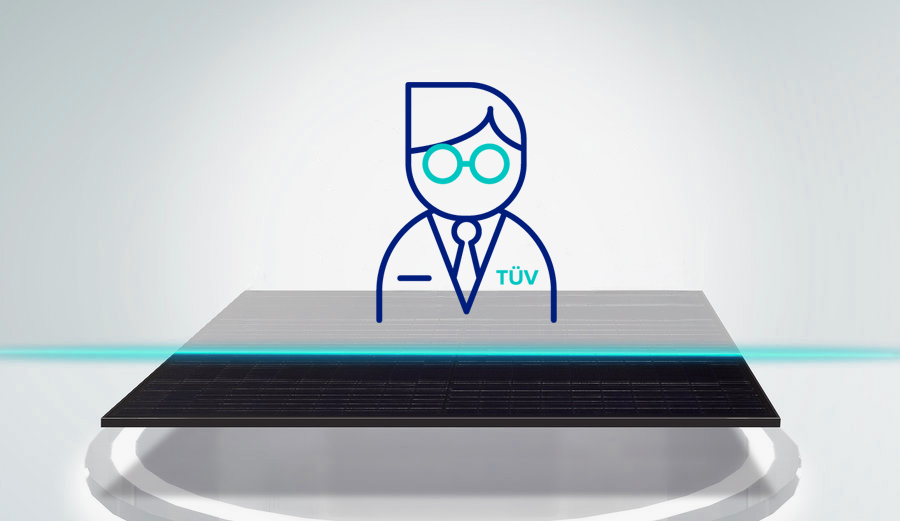
TÜV Rheinland employees test modules at all production sites
TÜV Rheinland employees are present at the production sites to monitor Qcells solar modules at all production sites via random sampling. They also witness the certification tests of the Qcells module test centres in Germany, Korea, Malaysia and China. As representatives of TÜV, they select the samples and monitor the tests.
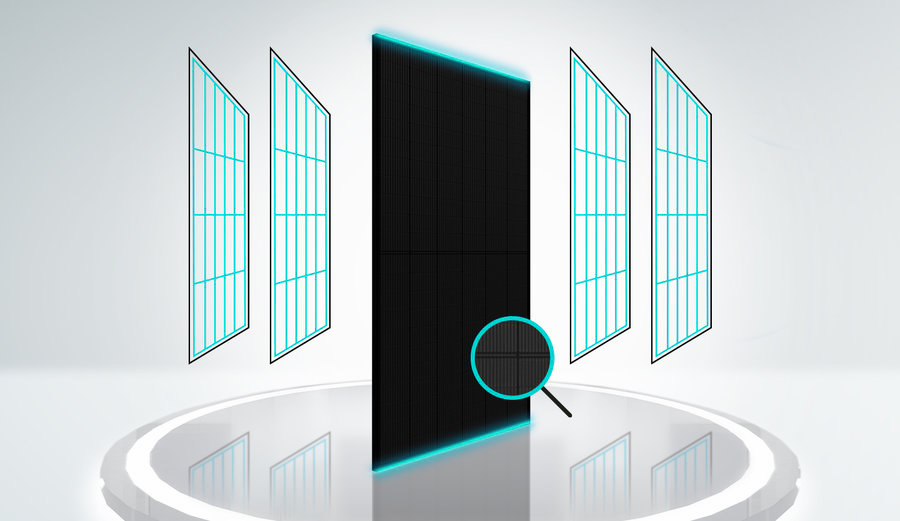
Scheduled random sample selection
To ensure that our solar module production can be regularly monitored, the TÜV Rheinland employee assigned to the relevant production site regularly takes random samples that are tested according to the strictest criteria. In this way, we ensure that all our product types are consistently tested worldwide.
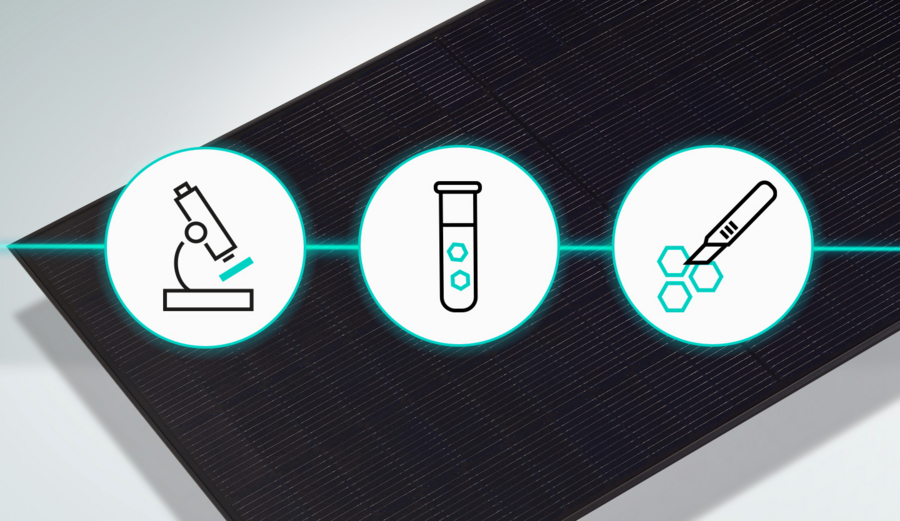
Random sampling of materials
Plastic components in particular are susceptible to wear and ageing. We therefore test materials from our suppliers that are classified as critical for durability, performance and safety, randomly on goods receipt before they are used in production, and regularly during production.
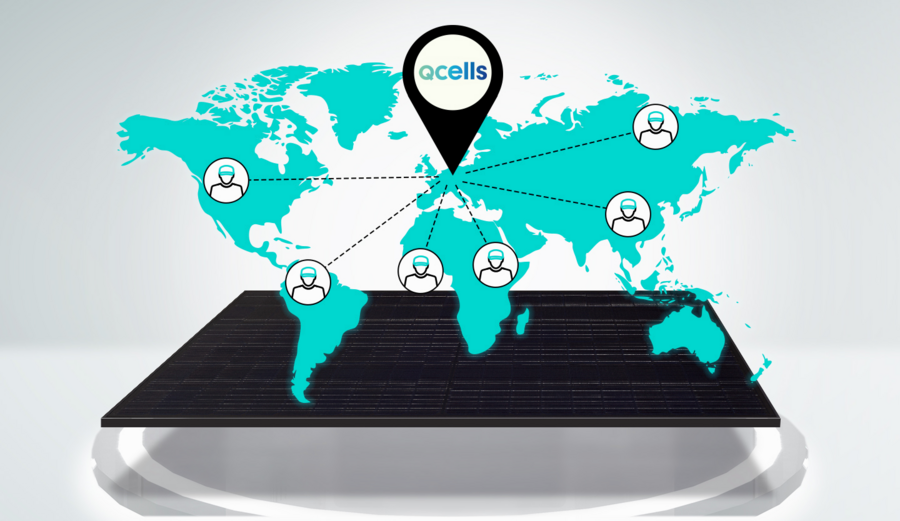
Supplier audits
We regularly check the material and component suppliers with regard to all critical components using a strict audit programme, paying particular attention to reliability and material properties as well as supplier change control.
To the point
We conduct this voluntary test initially for every new product and any product adaptation to ensure the reliability and long service life of our solar modules. Our test procedure goes far beyond the requirements of the basic certification and is many times tougher.
Independent TÜV Rheinland employees test solar modules from all production sites by random sampling and witness the certification tests at the international Qcells module test centres. As independent assessors, they are involved in the ongoing production monitoring.
TÜV Rheinland has added 3 additional requirements to the test catalogue – based on international standards – which go far beyond the standard approval and safety qualification:
- Implementation of an extended stress testing programme based on IEC TS 63209 to achieve high confidence in the reliability and long life of PV modules.
- Monthly random samples from the current production in order to be able to test and evaluate the regular quality and monitoring measures implemented by the manufacturer.
- Monitoring of the manufacturer's material and supplier monitoring programme with special attention to reliability and material properties and supplier change control for all critical components.